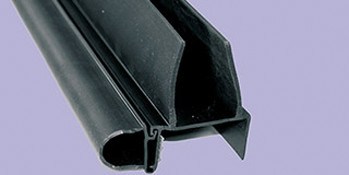
Exploring the Advantages of Plastic Extrusion for Custom Profiles
Custom components can be manufactured in multiple industries, including appliances, solar paneling, and more. The process is versatile for various products, such as customized profiles for consumer or automotive parts. At Clark and Rubber Plastic, our team specializes in high-quality processes that deliver precise and consistent results for small or large projects. Here are a few advantages of plastic extrusion for custom profiles:
Design Versatility
One advantage of plastic extrusion is its flexibility in design. The process helps produce complex cross-sectional profiles, allowing manufacturers to create custom shapes to meet exact specifications. Whether it’s for tubing, edging, seals, or intricate components, extrusion offers a variety of designs. Some products are made for airplanes or aerospace applications. Other options include automotive plastics, armaments, and solar plastics.
Material Options
Various material options suit any application. These materials include PVC, polyethylene, polypropylene, and thermoplastic elastomers. Each material offers unique features and advantages, such as flexibility, chemical resistance, durability, or temperature tolerance. Some applications might require lightweight materials for easier handling and durability in tough conditions. At Clark and Rubber Plastic, our team of experts helps select the best material for performance requirements and industry standards. Whether the focus is on strength or weather resistance, we’ll assist with a solution.
Quality and Performance
Consistency is key when manufacturing custom profiles, like automotive or military. Components used in the military are produced to a high standard so that they remain durable during daily use in harsh conditions. Minor variances may impact product performance. Plastic extrusion provides a steady, repeatable output that makes sure there is uniformity across every piece produced. Advanced equipment and quality control processes can offer tight tolerances and reliable performance. Other options include a balance of strength and weight. From cable trays for solar panels to sealing solutions in military equipment, custom extrusion helps deliver strength, durability, and longevity.
Custom Finishes
Another advantage of plastic extrusion is the ability to customize finishes and include additives. This includes UV stabilizers, flame retardants, color matching, and texture adjustments. These features may be incorporated during the extrusion process. Each product can be visually appealing and optimized for its intended use.
The extrusion process can be compatible with a wide range of secondary options. This includes how profiles may be cut, punched, drilled, coated, or assembled into more complex components. These custom secondary services include precision die-cutting, CNC turning, milling, and other additional processing. This integrated approach helps simplify supply chains to enhance the functionality of a finished product.
Use Plastic Extrusion With Clark and Rubber Plastic
At Clark and Rubber Plastic, our team has years of experience in plastic extrusion services, supporting a wide range of industries. Our team can create custom profiles to match exact requirements. Whether clients need small batch products, support for design refinement, or processing to meet product requirements, our team helps deliver. We combine state-of-the-art technology and hands-on craftsmanship to create a wide range of products, including sealants. Contact us today to learn more about the advantages of custom extrusion processes and how we can create a product for your project.
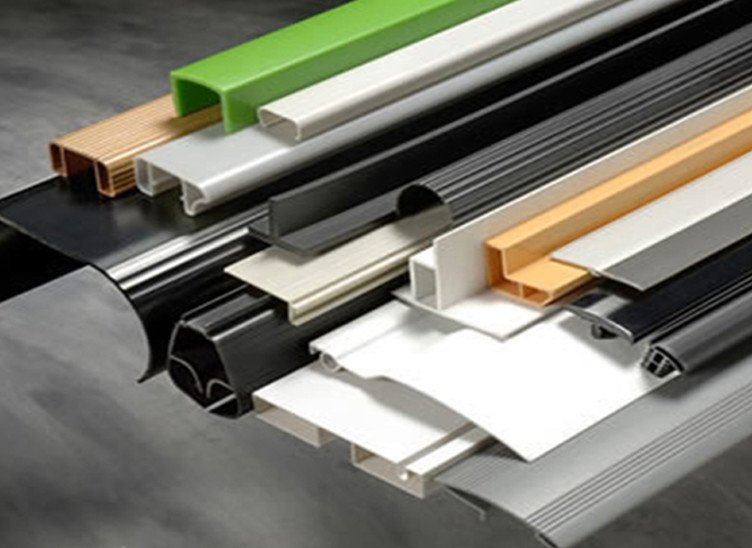
Unique Applications of Plastic Extrusion Across Industries
Plastic extrusion is a manufacturing process used in several industries, including automotive parts and appliance components. It involves creating high-quality plastic components like gaskets. Whether for military-grade applications or appliances, each tailored item can serve various purposes. At Clark and Rubber Plastic, we specialize in precision plastic extrusion, offering solutions for different industries. Here are some unique applications of the process:
1. Automotive Industry
Components created by Plastic extrusion help companies in the automotive industry make quality vehicle elements. This includes high-performance parts that withstand heat and wear and tear. Extruded pieces, like rubber inserts, contribute to more modern, lightweight designs. If a vehicle weighs less, it can improve fuel efficiency for the driver and reduce production costs for the manufacturer. Seals and weatherstripping are other applications that are extruded, and they prevent water, dust, and noise from entering vehicles. Wire harness tubing protects electrical writing from extreme heat or cold temperatures. Other components, such as dashboards, are custom-made for durability.
2. Appliance Industry
Modern appliances, such as refrigerators, can use extrusion for functional parts for items like door gaskets, which are airtight seals. These parts help improve energy efficiency and regulate the internal temperature to keep stored food safe for consumption. Other covered parts are flexible wire and cable insulation. This keeps the wire’s electrical components safe and secure. Here are some other appliance parts:
- Ice maker dispensers
- Trim and edging
- Hoses and tubing
- Casings
3. Consumer Industry
Protective covers for daily consumer products like food or cosmetics may help store them safely for a period of time. Packaging materials help prevent airborne contaminants or bacteria from entering these items, making them unsafe for customers. Environment-resistant covers include shields that also limit damage to electronic devices. With advanced techniques, Clark and Rubber Plastic manufacturers help produce high-quality, durable products to help other product-based companies be successful.
4. Military and Defense Industry
Extruded pieces used for military applications are required to have durable properties. These include components for airplanes, tanks, aerospace insulation, armaments or munitions, and more. As military members may be in life-threatening situations, components need to perform as expected and on demand. Parts should also be capable of keeping out sand, dust, and mud. Custom military parts provide higher levels of functionality and quality, such as for marine vessels like aircraft carriers, ships, submarines, and sonar buoys.
5. Solar Industry
Plastic and rubber items, such as clamps or rubber inserts, are designed for solar operations. These are customized to be sturdy, efficient, and resilient for solar panels that undergo extreme temperature fluctuations. Professionally developed wire management systems keep cords organized and secure. Other sealing solutions, like cable trays or inserts, prevent moisture and dust from damaging components.
Using plastic and rubber materials, our Clark and Rubber Plastic team implements materials such as EPDM (Ethylene Propylene Diene Monomer), TPV (Thermoplastic Vulcanizates), or SBR (Styrene Butadiene Rubber). Other plastics might include Viton®, HDPE, or Polycarbonate. We use a full range of thermoplastics and other materials, including RPVC, Provista, Sarlink, ASA, for customized parts.
Use Plastic Extrusion With Clark and Rubber Plastic
At Clark and Rubber Plastic, our manufacturing process serves multiple industries, including healthcare and medical machinery. We also provide custom solutions for construction, plumbing, electronics manufacturers, and industrial productions. Our plastic extrusion process helps enhance components’ durability, efficiency, and performance. Contact our team today to learn how we can custom-design parts or meet your business’s unique needs.
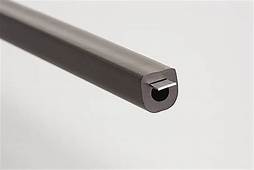
How to Customize Plastic Parts Using Extrusion Techniques
Manufacturers can use plastic extrusion to create plastic components for the solar, appliance, automotive, and military industries. This includes wire insulation and pipes. Clark Rubber & Plastic offers plastic and rubber extrusion services. Here are several ways to customize plastic parts with extrusion techniques:
Unique Molds for Die Cutting
The plastic extrusion process works by melting plastic pellets and pushing the material through a metal die. Metal dies have sharp, high-precision blades that cut and shape the plastic. A cold water bath cools the plastic, and the sizing belt and blade cut the plastic into individual parts. Die cutting can be used with multiple types of plastic, including polyethylene and polyvinyl chloride.
The metal die shapes the plastic according to specific dimensions. A plastic manufacturer can create a customized die mold that aligns with your particular product requirements. Using a unique die allows manufacturers to create customized plastic shapes for various industries and uses. This includes the distinctive shapes required for product packaging and the casing and seals for appliances. It also allows the manufacturer to create specialty parts. Clark Rubber & Plastic offers customized die molds and precision die-cutting services.
Custom Colors for Products
Colorants are mixed into the raw materials to color a plastic extrusion product. The melting process allows the plastic pellets to combine with colorants. This coloring process allows all the parts to be the same color, creating a uniform appearance. You can choose a custom color for your products. We can also combine multiple colors in a single project.
Co-Extrusion Process for Different Materials
Different materials have varying thicknesses and durability. Using two or more materials in a plastic component allows you to build a complex product with multiple properties. The co-extrusion process can help you customize the component to fulfill the necessary performance requirements, such as enhancing the component’s strength and sturdiness. This can be helpful when creating plastic parts used in military vehicles and armaments. These parts are held to high standards for durability, as they are required to withstand extreme conditions. Our high-quality production system helps make sure all of our products meet high safety and production standards.
Co-extrusion also allows manufacturers to combine two polymers into a cross-section to create different layers. The materials are extruded at the same time. The extruding machines can be set to various speeds to change the layers’ thickness. We can also combine three polymers through tri-extrusion, which uses three extrusion processes. Our team members at Clark Rubber & Plastic offer recommendations on what type of materials are appropriate for your product.
Plastic Extrusion at Clark Rubber & Plastic
We use tubing, blow film, and sheet extrusion processes to create uniform tubes, thin films, and plastic sheets. From prototyping to high-level production, Clark Rubber & Plastic provides fast turnaround times for plastic extrusion projects. We also offer milling, digital printing, and packaging services for your products. An online form is available on our website to request a quote. To learn more about the extrusion techniques at Clark Rubber & Plastic, call us today.
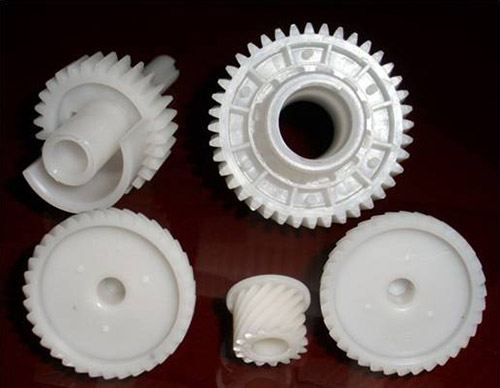
Three Questions To Ask Your Rubber and Plastic Manufacturer
A rubber or plastic manufacturer can help you create a high-quality custom rubber or plastic product. Services at Clark Rubber and Plastic include custom plastic and rubber molding. Here are three questions to ask your manufacturer:
1. What Are Your Capabilities and Services?
When deciding on a manufacturer for your product, make sure that they offer the production services you require for your project. Ask them about their plastic and rubber molding capabilities, as well as extrusion services. Clark Rubber and Plastic provides precision die-cutting to meet product specifications. Our plastic and rubber extrusion processes offer a wide variety of textures and thicknesses, and our custom plastic injection and rubber molding process allows us to create custom parts and products.
See if your manufacturer offers additional services, such as milling and packaging. This allows you to work with one manufacturer for your product instead of multiple suppliers, simplifying the process and reducing production time. We offer digital printing and milling at Clark Rubber and Plastic. Our taping services include heat-activated tape services for packaging and product needs.
2. What Kind of Product Runs Do You Offer?
Check with the manufacturer to see what their volume capabilities are. Ask about:
- Prototype production: If you are making a prototype for your product, ask your manufacturer to see if they offer low-volume services.
- Size of the facilities: For a longer product run, see if the facility has the equipment and the space to undertake larger projects successfully.
- Production rate and times: Check to see if the projected production rates, turnaround, and lead times fit with your project schedule.
Our 40,000-square-foot plastic operations facility and our high-quality equipment and tools at Clark Rubber and Plastic enable us to offer both long and short product runs. Our computer numerical control processes allow us to provide fine details and high levels of accuracy for products of all sizes. We can take on projects of various complexities and sizes. We also help you stay on schedule with a faster turnaround time.
3. What Quality Standards Do You Follow?
Make sure the manufacturer you are working with can meet your industry’s product standards. Depending on industry requirements, plastic and rubber products should be able to withstand:
- High temperatures
- Constant use
- Extreme weather conditions
We are dedicated to providing high-quality plastic and rubber extrusion products. Clark Rubber and Plastic has developed a quality control system that we follow to make sure that all our products meet high production standards and safety requirements. We utilize certified high-quality materials for our components and products to provide structural integrity and durability.
Contact a Plastic and Rubber Molding Manufacturer
The industries we provide products for include the automotive, appliance, consumer, military, and solar industries. We utilize precision machinery, and we can also work with metals, such as steel. You can request a quote for our plastic and rubber molding and other available services through our online form. If you are interested in partnering with Clark Rubber and Plastic, we invite you to call or email us today.
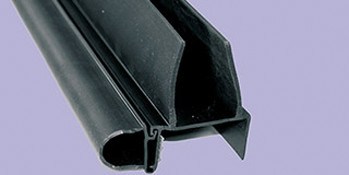
4 Reasons To Use Plastic Extrusion Services
Plastic extrusion allows companies across many industries to create custom parts for their products. At Clark Rubber and Plastic, we offer extrusion services to help customers create plastic goods of various colors, textures, thicknesses, and hardnesses. Here are four reasons to use plastic extrusion services:
1. Product Consistency
Outsourcing your plastic part production to an extrusion professional allows you to achieve consistency across all batches. You can give a plastic manufacturer your plan, and they will create parts to match your specifications. At Clark Rubber and Plastic, we have extruders with instrumentation that measures the plastic’s temperature and thickness to maintain consistency across all products. This machinery also detects the pressure of the extruder screw to confirm each part is produced at the same rate with the same amount of force.
2. Precise Dimensions
A plastic extrusion company creates custom dies for each of your parts. The die is a metal disc that has custom shapes cut into it. Melted plastic moves through the die and cools to create the unique shape or profile your company needs. The high-precision tolerance levels in our machines result in products with dimensions that closely match their original manufacturing plans. Before creating your die and beginning production, our team will discuss your product’s application and recommend design changes and material types that will make your final products as effective as possible.
3. Customization Options
Producing plastic parts with extrusion allows you to customize the final product’s size, density, and color. We carry a range of plastic types to provide customers with options for the flexibility and durability of their final product. Clark Rubber and Plastic offers military-grade and UL-approved materials to confirm the quality of your components. We can combine materials of various colors and properties to produce a fully customized part.
Our dual-durometer production process involves combining two plastic types with varying hardness levels to achieve a final product with the characteristics of both materials. Components made with dual-durometer extrusion include seals, impact absorbers, and sound dampeners. Our team assesses your project goals to help you determine which plastic type and production method is right for you.
4. Quick Production
Extrusion services speed up the manufacturing processes by assigning a key task to a professional facility that handles high-volume orders. Once you receive your custom parts, your team is only responsible for assembling and packaging the final products. At Clark Rubber and Plastic, we use extruders with barrels and tips that hold large batches of melted plastic and automatically direct it into the die. This machinery allows us to produce high-volume orders of plastic parts and prototypes.
Explore Plastic Extrusion Services
Clark Rubber and Plastic offers extrusion services to help companies produce custom profiles, shapes, and forms. We use a variety of plastic materials, including RPVC, neoprene, acrylic, and nitrile. Our facility has multiple extrusion lines that allow us to produce high-quality products quickly. Contact us today to learn more about our plastic manufacturing services and receive a free quote for your extrusion project.
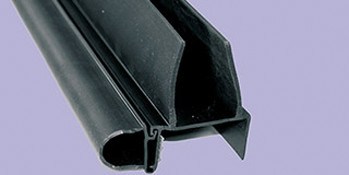
Two Finishes for Your Extruded Plastic Products
The plastic extrusion process is used to produce products for the consumer, military, automotive, and solar panel industries. Our company, Clark Rubber & Plastic, offers extruded plastic products with high-quality surface finishes. Here are two types of finishes for plastic products:
Extrusion Process
The plastic extrusion process allows us to create customized, versatile plastic products of different shapes and profiles. It begins with melting the plastic pellets. The types of plastic we use include PVC, acrylic, and polyethylene. During the melting process, Clark Rubber & Plastic is able to add colorants and stabilizing materials to the mixture.
The mixture is pushed through a die to shape the material. Coextrusion and tri-extrusion techniques can be used during the shaping process, impacting the outer layers of the plastic. These techniques extrude two or three materials at the same time. This process allows different materials and colors to be added to the plastic, creating complex products with a variety of properties. These properties include barrier properties and strength.
After we shape the plastic with the die, we cool it using a cold water bath. Our belts size the profile according to the client’s needs. A blade cuts the material into individual pieces at the end of the belt.
1. Clear Finish
A clear or transparent finish can be used for completed plastic products. This finish may apply to plastic packaging products. Clark Rubber & Plastic uses extrusion to create sheets and films of various thicknesses for packaging materials. Clear plastic materials protect the product while allowing consumers to see what the product looks like, creating greater visual appeal for the product.
2. Crosshead Extrusion Coating
If a product needs reinforcement, Clark Rubber & Plastic can use the extrusion crosshead technique to apply a finish. This technique involves running the material through a 90-degree crosshead. At the same time, the finish is applied to the material to make it stronger. Crosshead extrusion coating is a durable finish that can be used with textiles, such as thermoplastics. It can also be used for some fabrics, other textiles, and metal materials.
Clark Rubber & Plastic can work with EPDM, ABS, LPDE, and other materials for extrusion coating. This finish offers a waterproof layer to the material or creates additional protection for the inner materials. It can also be used to provide a decorative exterior for the product. This coating is used for wire coating extrusion, cable, and other products.
Plastic Extrusion at Clark Rubber & Plastic
We offer precision die cutting and use custom dies during the extrusion process. Our plastic products include slide-outs, inserts for solar applications, and automotive tubing for vehicle air and fuel systems. We also offer military-grade parts that can withstand extreme conditions.
Clark Rubber & Plastic also offers injection molding, rubber products, milling, CNC turning services, and precision machining. Our company uses a quality system to ensure that all our products and services meet high production and safety standards. To learn more about plastic extrusion and our other services, we invite you to contact Clark Rubber & Plastic today.

7 Industries That Use Plastic and Rubber Molding Services
Plastic and rubber molding services play a key role in many manufacturing processes for various industries. Each industry depends on materials made from molding processes to increase the functionality of its products. At Clark Rubber and Plastic, we manufacture high-quality materials that meet our clients’ demands. Here are seven industries that use molding services:
1. Automotive
The automotive industry uses plastic- and rubber-molded products to produce components that enhance a vehicle’s safety, performance, and comfort. These products include tires and seals to prevent flat tires while driving. Interior and exterior elements include bumpers, door panels, and interior trims. Engine parts like hoses, belts, and mounts support the engine and are heat resistant. Manufacturers also use rubber and plastic moldings for electrical wiring coverings.
2. Healthcare and Medical Equipment
Healthcare industries rely on rubber and plastic molding products to produce safe, sterile components for patient care and medical advancements. These include medical devices such as ventilators, blood pressure monitors, and diagnostic equipment. Other products, such as surgical instruments, use rubber for sterile solutions. Manufacturers use custom-molded materials to make lightweight prosthetic and orthotic devices.
3. Consumer Goods
Rubber molded products are designed for everyday household items, such as kitchen utensils and tools like silicone baking molds. Many toys are rubber-molded to make sure they are child- or user-friendly. Soles and inserts in footwear are often molded from rubber to be slip-resistant while providing comfort. Other household moldings contribute to personal care products and their ergonomic design.
4. Electronics and Electrical
Plastic and rubber molding services create protective coverings for wires to resist environmental factors like heat and moisture. Plastic moldings are also used to make connectors, sockets, and plugs to house wiring connections and prevent the wires from touching. This can prevent sparks. Household electronic devices contain lightweight molded pieces to protect components from dust, water, and other contaminants.
5. Construction and Infrastructure
In construction, piping and fittings use rubber gaskets to seal plumbing and water management systems. Rubber molding services also create seals for windows, doors, and HVAC systems for weatherproofing and maintaining energy efficiency. Plastic and rubber are necessary to produce personal protection gear such as safety boots, gloves, and eyewear.
6. Renewable Energy
Engineers use molded rubber seals in dams and turbines to make sure they are water-tight. Rubber hoses are utilized because they can withstand extreme temperatures and pressures. Plastic framing protects solar panels from environmental conditions.
7. Aerospace
Components on aircraft, such as shock absorbers and fuel system parts, are from rubber molding services. Even items inside the aircraft, like tray tables and door handles, are built from moldings. These parts are durable enough to withstand changes in air pressure during take-off and landing.
Schedule Rubber Molding Services Today
Plastic and rubber molding services are used in industries worldwide, offering durable and lightweight materials. Our rubber molds support natural rubber, neoprene, and nitrile. From vehicle safety and medical equipment to everyday household products, molding services are integral to manufacturing. At Clark Rubber and Plastic, we deliver top-quality molding services to fit your needs. Call us today to schedule production for your next project.
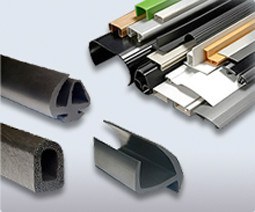
How To Choose the Right Company for Your Next Extrusion Project
The extrusion process allows custom products to be manufactured for a variety of projects. Clark Rubber & Plastic is a manufacturer that offers rubber and plastic extrusion services. Here are several things to look for when choosing a company for your extrusion project:
Meets Product Requirements for Industries
Find a company that offers rubber and plastic extrusion products that meet industry standards. Appliances that require rubber and plastic products should withstand regular usage and high temperatures. In a military environment, rubber and plastic components are expected to meet strict regulatory compliance standards to endure extreme conditions and provide constant reliability. Rubber and plastic components also help uphold the structural integrity of solar equipment. Look for a manufacturer that prioritizes using high-quality materials during the extrusion process and creating long-lasting components.
Clark Rubber & Plastic serves the appliance, automotive, consumer, military, and solar industries. We utilize a quality system as part of all company operations to make sure that our products meet your industry’s production and safety requirements. We use certified materials and provide uniform density and structural integrity for our high-quality products. Clark Rubber & Plastic has received a UL certification of compliance for QMFZ2.E356537 Plastics-Component.
Handles Long and Short Product Runs
When selecting a company for extrusion products, check their manufacturing and production volume capabilities. If you are creating a prototype or a single product, see if the company offers short product runs. If your project requires a longer run, talk to the company about their facilities and rate of production. Ask about turnaround and lead times to make sure the company’s production process aligns with your project timeline.
Our manufacturing plant can manage all project sizes and complexity levels. Clark Rubber & Plastic can provide a variety of profiles and shapes for your plastic and rubber extrusion products. With six newer extrusion lines and a 40,000-square-foot facility dedicated to plastic operations, we provide both high- and low-volume production services and offer a quick turnaround time.
Provides a Variety of Services
Find a manufacturer that provides multiple services, such as assembling, milling, and packaging. This allows you to work with a single company to fulfill your project needs, which can help reduce production time. You will not need to work with multiple suppliers to complete one project. Clark Rubber & Plastic creates our own tooling with state-of-the-art equipment. Our die-cutting services allow us to meet precise specifications for different products. Clark Rubber & Plastic’s other services include custom CNC turning, digital printing, taping, kitting, and milling.
Plastic Extrusion Services at Clark Rubber & Plastic
We incorporate equipment that utilizes multiple plastic extrusion techniques, allowing us to combine two to three materials with different properties. Extrusion products we offer include rubber seals and tubing, solid-cored profiles, and plastic tubing and sleeves. Our team at Clark Rubber & Plastic will discuss your project needs with you, going over the project requirements and industry specifications. We can also recommend materials and make design suggestions. We invite you to call us today or request a quote for our rubber or plastic extrusion services.
- 1